Ontdek hoe kwaliteitsvolle materialen, ervaren vakmanschap en uitgebreide testen het grote verschil maken.
In onze hedendaagse wereld is vaak handen wassen een nieuwe gewoonte geworden: een eenvoudige maatregel voor de hygiëne die ons helpt om gezond te blijven. Deze toename in het handen wassen betekent dat kranen elke dag aan meer slijtage onderhevig zijn. Duurzaamheid van kranen is dan ook nog nooit zo belangrijk geweest.
Messing speelt een belangrijk rol in de duurzaamheid van kranen
Messing is een belangrijk bestanddeel van kranen, en niet om het even welke messing. Wegens de verschillende zuurtegraad van leidingwater, verzekert weerstand tegen ontzinking een grote duurzaamheid van elke kraan, ongeacht waarvoor die bestemd is.
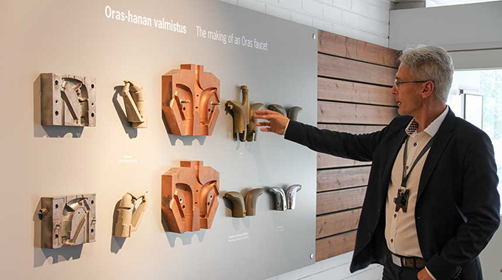
“In de vestiging van Rauma in Finland worden elke dag gemiddeld 3.000 kranen gemaakt. Eén procent van deze kranen ondergaan een steekproef voordat ze worden ingepakt en wereldwijd verzonden.”
Marko Sundholm
Nordic Sales Manager van de Oras Group
Een fantastische kraan begint met een fantastisch ontwerp en een nauwgezette planning
Op basis van het uiteindelijke ontwerp dat via een computer gesimuleerd wordt en de gegoten prototypes, gaat het goedgekeurde product in productie, in een mix van geautomatiseerde en handmatige processen.
Productiestappen van de kraan
- Opbouw van de kern
- Gieten
- Zagen
- Machinale bewerking
- Slijpen
- Polijsten
- Bekleding met chroom
- Assemblage
- Testen
Elke stap van de productielijn biedt een kans om een eindproduct te produceren dat ontworpen en gebouwd is om lang mee te gaan.
Opbouw van de kern
De kern heeft betrekking op de waterleidingen vanbinnen in de kraan. Tijdens het gieten wordt de kern gemaakt op basis van fijn zand en een uithardingsmiddel dat in een kernbox wordt verwarmd.
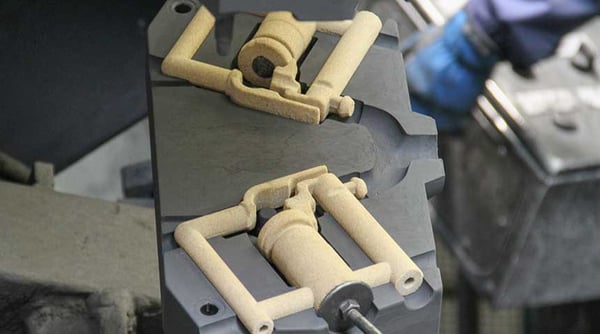
De kernen in de gietmatrijs zijn klaar voor het gieten
Gieten
Er wordt een gietsel gemaakt van de kraanrompen op basis van onze speciale messing staven bestand tegen ontzinking. De schelpmatrijzen worden ondergedompeld in een oplossing van water en grafiet door een werknemer, die als “metaalgieter” wordt aangeduid, die de kern in de matrijzen plaatst nadat los zand werd verwijderd.
Vervolgens worden de matrijzen gedicht en in een zeer hete gietoven gedaan, waar drie ton gesmolten messing in de schelpmatrijzen stroomt.
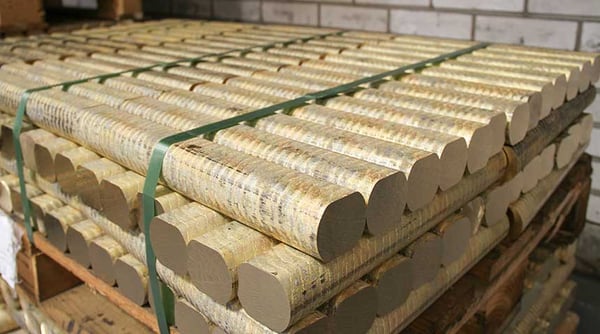
Messing staven bestand tegen ontzinking
Zagen
Zodra de gietsels zijn verwijderd en afgekoeld, wordt de kern uit de kraanrompen gehaald door die te laten wervelen in een molen met metalen balletjes. Vervolgens worden de gekoelde kraanrompen los van elkaar gezaagd en worden onnodige delen verwijderd.
Machinale bewerking, slijpen en polijsten
De kraanrompen worden op een transportband geplaatst en doorlopen ze de processen voor machinale bewerking, slijpen en polijsten: deze processen maken de buitenkant perfect effen. Daarna wordt elke kraan handmatig gecontroleerd, om na te gaan of ze aan de strengste normen voldoen. Kleine onvolkomenheden worden handmatig opgelost.
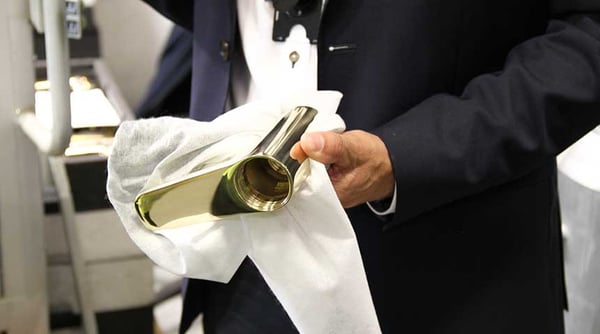
“De oppervlakken van het product moeten onberispelijk zijn voordat die met chroom worden bekleed, omdat chroom een genadeloos materiaal is. In plaats van te bedekken, zal het ook maar de kleinste foutjes gaan benadrukken.”
Bekleding met chroom
Tijdens de laatste productiefase wordt de bekleding met chroom aangebracht, zodat de kraan een hard, glanzend en slijtvast oppervlak heeft. Een stap die bijzondere aandacht vereist, aldus Marko Sundholm.
Dit gebeurt met de nodige zorg om de kraanrompen niet met blote handen aan te raken, zodat er geen vingerafdrukken op het oppervlak zitten.
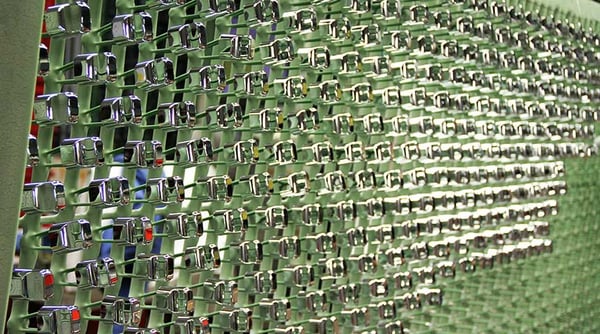
De puzzel afwerken
De kranen bevatten ook onderdelen van kunststof en composiet, waarbij zichtbare onderdelen met chroom worden bedekt. Het werken met onderdelen van kunststof kan een grotere uitdaging vormen in vergelijking met messing omdat zij eerst met een koperlaag worden bedekt, vervolgens met een nikkellaag om het oppervlak tegen thermische expansie te beschermen, en ten slotte met chroom.
Bekleding met chroom duurt grofweg twee uur, waarbij de kranen tot 40 keer worden ondergedompeld en gewassen. Na de bekleding met chroom worden markeringen met een laser aangebracht, bijvoorbeeld het logo van het merk. Daarna worden de kranen grondig geïnspecteerd en geassembleerd.
Testen
Elke kraan moet aan verschillende vereisten beantwoorden voordat het op de markt kan worden gebracht. Om bijvoorbeeld het geluidsniveau te testen, worden de kranen in een drijvende, geluidsdichte kamer van beton geplaatst, om te controleren of ze een bepaald volume niet overschrijden. De laatste stap in het proces is de steekproef. Wij voeren op 1 % van ongeveer 3.000 kranen die elke dag in onze fabriek in Rauma worden gemaakt, een steekproef uit.
Nu zijn onze duurzame en deskundig gemaakte kranen klaar om ingepakt en naar de verkopers en hun eindbestemming verzonden te worden: woningen, ziekenhuizen, scholen en andere gebouwen over de hele wereld.
