Guarda come i materiali di qualità, il lavoro esperto e i test approfonditi fanno la differenza.
Nel mondo di oggi, lavarsi le mani più frequentemente è diventato la nostra nuova normalità - come una semplice misura igienica per aiutarci a mantenerci in salute. Questo aumento del lavaggio delle mani significa che i miscelatori devono gestire un'usura quotidiana più dura e la durata dei nostri prodotti è più importante che mai.
L'ottone gioca un ruolo importante nella durata dei miscelatori
L'ottone è un componente importante per i miscelatori e in HANSA non usiamo un ottone qualsiasi.
A causa dei diversi livelli di acidità dell'acqua, la resistenza alla dezincificazione assicura la durata di ogni prodotto, indipendentemente dalla sua destinazione.
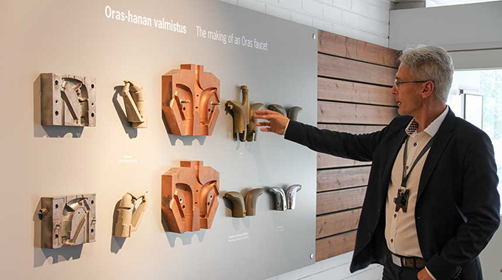
"Nello stabilimento di Rauma, in Finlandia, vengono prodotti in media 3.000 miscelatori al giorno. L'uno per cento di questi viene controllato a campione prima di essere confezionato e spedito in tutto il mondo".
Marko Sundholm
Oras Group’s Nordic Sales Manager
Un grande miscelatore inizia con un grande design e una pianificazione meticolosa
Dal design finale simulato al computer e dai prototipi fusi, il design del prodotto approvato passa alla produzione - fatta di un mix di processi automatizzati e manuali.
Fasi di produzione del miscelatore
- Costruzione del nucleo
- Colata
- Taglio
- Lavorazione
- Rettifica
- Lucidatura
- Cromatura
- Montaggio
- Test
Ogni passo della linea di produzione offre la possibilità di produrre un prodotto finale progettato e costruito per durare a lungo.
Corpo centrale
Il nucleo é tutta la parte interna del miscelatore. Durante la fusione, il nucleo viene creato usando sabbia fine e un agente indurente riscaldato in uno stampo.
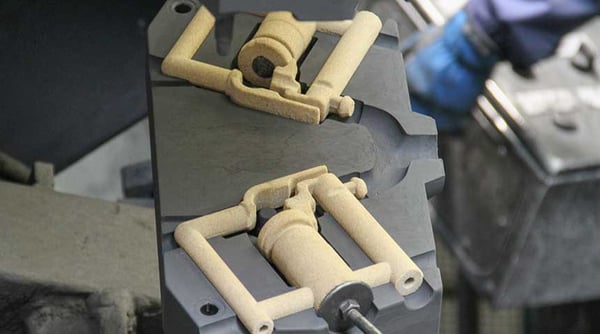
The corpo interno dentro lo stampo, pronto per la fusione
La fusione
Una colata dei corpi dei miscelatori è fatta dalle nostre speciali barre di ottone resistenti alla dezincificazione. Gli stampi a conchiglia sono immersi in una soluzione di acqua e grafite, in questa fase, un operaio specializzato - chiamato "fonditore" - posiziona l'anima all'interno degli stampi dopo aver rimosso la sabbia in eccesso.
Gli stampi vengono poi sigillati e messi nel forno di colata bollente, attraverso il quale tre tonnellate di ottone fuso fluiscono negli stampi a conchiglia.
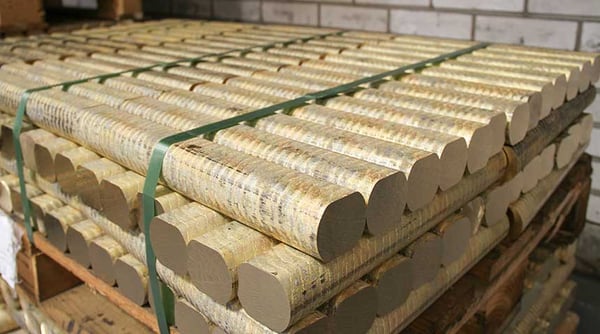
Barre di ottone resistenti alla dezincatura
Taglio
Una volta che le parti fuse sono state rimosse e raffreddate, il nucleo viene rimosso dai corpi dei miscelatori facendoli turbinare in un mulino dotato di sfere di metallo. I corpi dei miscelatori raffreddati vengono poi tagliati, rimuovendo anche le parti non necessarie.
Lavorazione, rettifica e lucidatura
Posizionati su un nastro trasportatore, i corpi dei miscelatori passano attraverso processi automatizzati di lavorazione, rettifica e lucidatura - ottenendo un esterno liscio. Ogni prodotto viene poi controllato a mano per assicurarsi che soddisfi i più alti standard - correggendo manualmente qualsiasi piccola imperfezione.
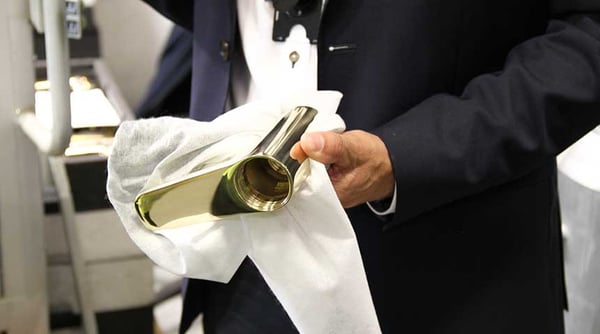
"Le superfici dei prodotti devono essere impeccabili prima della cromatura, perché il cromo è un materiale spietato. Non copre, ma piuttosto evidenzia, anche il più piccolo dei difetti".
Cromatura
La fase finale della produzione prevede la cromatura, creando una superficie dura, lucida e resistente all'usura.
Un passo che richiede molta attenzione, dice Marko Sundholm.
Questo viene fatto assicurandosi che i corpi dei miscelatori non vengano toccati a mani nude - in modo che le impronte digitali non appaiano sulla superficie.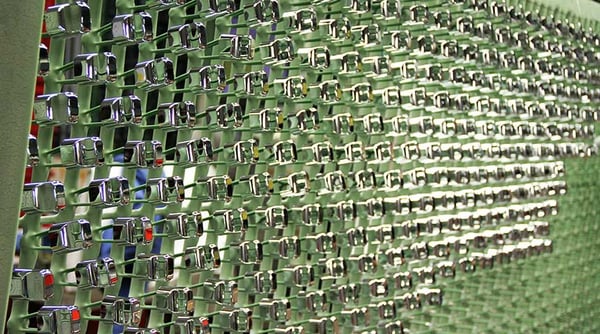
Completamento del puzzle
Alcuni miscelatori vengono assemblati con parti in plastica e composite e con i componenti visibili cromati. Lavorare con le parti in plastica può essere più impegnativo che con l'ottone, perché vengono placcate con uno strato di rame, poi uno strato di nichel per proteggere la superficie dall'espansione termica e infine il cromo.
La cromatura richiede circa due ore e comprende l'ammollo e il lavaggio dei rubinetti fino a 40 volte. Dopo la cromatura, tutte le marcature come il logo del marchio vengono aggiunte con il laser, e i miscelatori accuratamente controllati e assemblati.
Test
Ogni miscelatore deve soddisfare una serie di requisiti prima di poter entrare sul mercato. Per esempio, per testare il livello sonoro, i miscelatori vengono messi in una stanza di cemento galleggiante insonorizzata per assicurarsi che non superino un certo livello
L'ultimo passo di questo processo è il controllo a campione. Dei circa 3.000 miscelatori che vengono prodotti ogni giorno nella nostra fabbrica di Rauma, effettuiamo controlli a campione sull'1%.
A questo punto, i nostri prodotti, resistenti e realizzati con maestria, sono pronti per essere imballati e spediti ai rivenditori e alla loro destinazione finale - nelle case, negli ospedali, nelle scuole e in altri edifici di tutto il mondo.
