See how quality materials, expert craftsmanship and extensive testing make all the difference.
In today’s world, more frequent handwashing has become our new normal – as a simple hygienic measure to help keep us healthy. This increase in handwashing means faucets need to handle tougher everyday wear and tear, and the durability of faucets is perhaps more important than ever.
Brass plays a major role in the durability of faucets
Brass is an important component to faucets and not just any brass. Due to the varying levels of acidity in tap water, dezincification-resistant ensures the long-lasting durability of every faucet – no matter its destination.
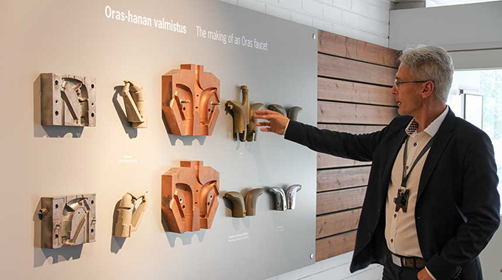
“An average of 3,000 faucets are manufactured at the Rauma, Finland plant every day. One per cent of these are spot-checked before being packaged and shipped around the world.”
Marko Sundholm
Oras Group’s Nordic Sales Manager
A great faucet starts with great design and meticulous planning
From the final computer-simulated design and the casted prototypes, the approved product design heads into production – made of a mix of automated and manual processes.
Faucet production steps
- Core building
- Casting
- Sawing
- Machining
- Grinding
- Polishing
- Chrome plating
- Assembly
- Testing
Every step of the production line offers a chance to produce an end-product designed and built for longevity.
Core building
The core refers to the waterways within the faucet. During casting, the core is made using fine sand and a hardening agent heated in a core box.
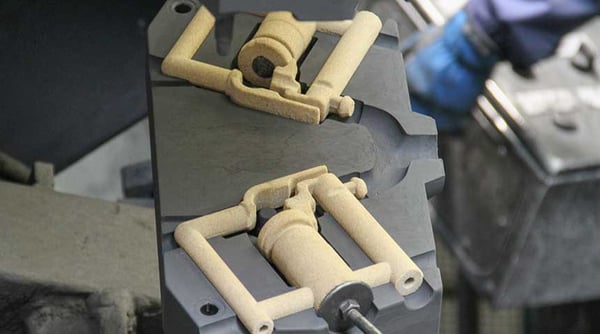
The cores inside the mould ready for casting
Casting
A casting of the faucet bodies is made from our special dezincification-resistant brass bars. The shell moulds are dipped into a water and graphite solution with an employee – referred to as a “caster” – placing the core inside the moulds after removing any loose sand.
The moulds are then sealed and placed in the blazing hot casting furnace, through which three tons of molten brass flow into the shell moulds.
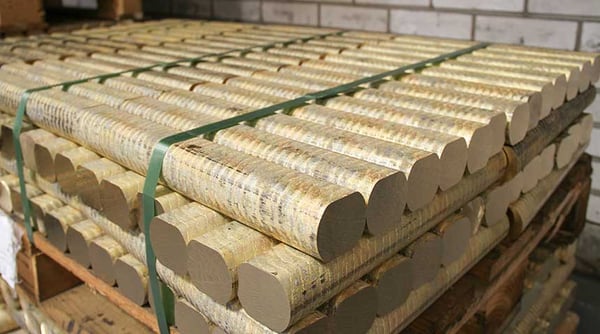
Dezincification resistant brass bars
Sawing
Once the casts have been removed and cooled, the core is removed from the faucet bodies by whirling it in a mill equipped with metal balls. Cooled faucet bodies are then sawed apart, with unnecessary parts also being removed.
Machining, grinding and polishing
Placed on a conveyor belt, the faucet bodies move through automated machining, grinding and polishing processes – resulting in a smooth exterior. Each faucet is then checked by hand to ensure they meet the highest standards – fixing any minor tweaks manually.
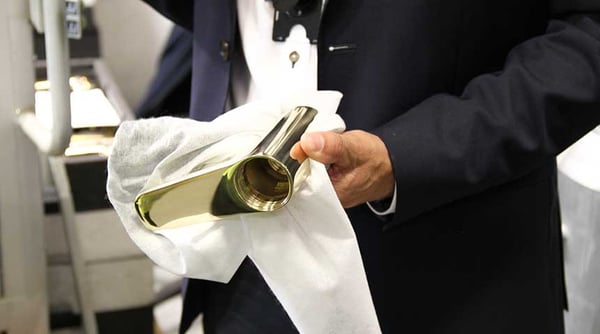
“Product surfaces need to be flawless before chrome-plating, as chrome is a ruthless material. It does not cover, but rather highlights, even the smallest of errors.”
Chrome plating
The final stage of production involves chrome plating, leaving each faucet with a hard, shiny and wear-resistant surface. A step which requires extra care, says Marko Sundholm.
This is done while ensuring that faucet bodies are not touched with bare hands – so that fingerprints do not show up on the surface.
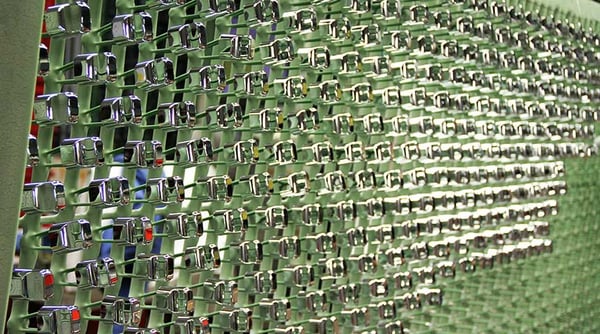
Completing the puzzle
Faucets are also built with plastic and composite parts, with the visible components being chrome plated. Working with plastic parts can be more of a challenge than brass as they are plated with a copper layer, then a nickel layer to protect the surface from thermal expansion, and finally chrome.
Chrome plating takes roughly two hours and includes soaking and washing the faucets up to 40 times. After chrome plating, any markings such as the brand logo are added by laser, and the faucets are thoroughly inspected and assembled.
Testing
Each faucet must meet a variety of requirements before it can enter the market. For example, to test the sound level, faucets are placed in a sound-proof, floating concrete room to ensure they do not exceed a certain volume. The last step in this process is the spot check. Of the approximately 3,000 faucets that are made every day in our factory in Rauma, we carry out random checks on 1%.
Now, our durable and expertly crafted faucets are ready to be packaged and shipped to sellers and on to their final destination – into homes, hospitals, schools and other buildings across the world.
